随着科学技术的不断进步,现代产品向着微型化和精密化发展。越来越多的微器件及微结构被应用于医疗、电子、新能源、国防等工业领域之中[1]。随之,特种加工技术的发展也是突飞猛进。德国马普研究所科学家Schuster等[2]发现,利用纳秒脉冲技术可以抑制杂散腐蚀,提高加工的定域能力,加工出轮廓结构清晰均匀的微米级零件。自此,微细电解加工技术成为本世纪最活跃的科学研究发展方向之一。
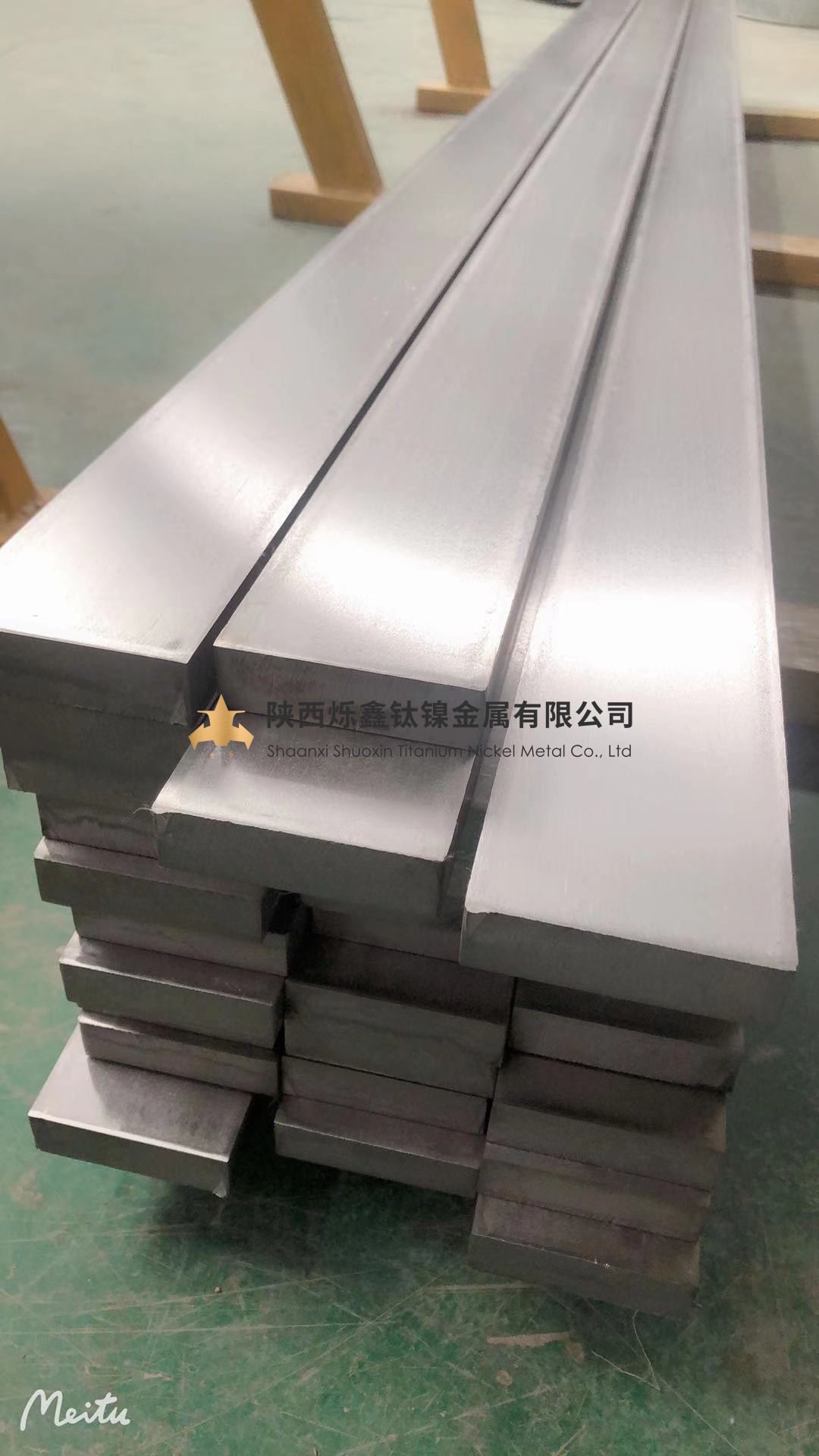
微细电解线切割技术也迅速发展起来,其具有成本低,加工表面无裂纹、无应力、精度高等优点[3]。微细电解线切割加工技术利用电化学原理,加工过程中,工件作为阳极失电子溶解,线电极作为阴极不会有材料的损耗,并且其与工件不会接触,加工出来的零件不会存在变形以及热影响区[4]。
许多学者都对此技术开展了相应的研究。日本学者R.Maeda研究在冲液情况下,电参数、工件厚度等对线电极极限加工速率的影响,并推导出进给速率方程[5-6]。王昆对微细电解线切割加工技术进行了深入研究,建立了微细电解线切割加工的理论模型,提出了在线制备线电极的方法[7],并探究了如何促进加工间隙内产物的排出。于洽提出了通过线电极往复运动和工件低频振动共同强化加工间隙内传质过程来提高微细电解线切割的切缝质量的方法[8]。李鹏提出了多线电极微细电解加工技术,通过使用多线电极能够大幅提高其加工效率[9]。童品周提出了多层工件叠加电解线切割加工方案,以此来提高电解切割加工的效率[10]。
由于要实现高宽深比结构加工,在缝宽无法无限减小的情况下,只能提高加工零件厚度。所以实现厚零件的微细电解加工非常有意义。南京航空航天大学在5mm的镍板上加工出臂宽为200μm,深宽比为20的悬臂梁结构,但其采用10.2V的直流电压进行微细电解线切割加工[11]。现国内利用超短脉冲进行微细电解加工,工件的厚度约为100μm。暂时还没有学者利用超短脉冲对较厚的零件结构进行微细电解线切割试验研究。
本文采用大电压的超短脉冲电源,在有效抑制杂散腐蚀的效果下,利用直径为10μm的钨丝,在厚度为800μm的厚镍板上进行微细电解切割,同时采用往复运丝的方法,加快加工区内电解产物的排出,并通过正交试验,研究加工电压、脉宽、周期、电解液浓度等4个因素对电解加工的影响。
1、原理及试验系统
1.1原理
微细电解线切割加工的原理图如图1所示。超短脉冲电源正极接工件,负极接线电极。采用电化学腐蚀原理,工件作为阳极失电子,材料被腐蚀溶解;线电极作为阴极,其周围电解液中H+得电子。
线电极按照预先设定的轨迹运动,加工出所需的轮廓特征结构。在加工过程中,为保证线电极周围的电解液中H+离子浓度得到及时更新补充,采用线电极往复运丝的方法,利用液体黏性,通过线电极的往复运动,带动电解液的流动,来促进电解产物的排出以及及时更新补充线电极周围H+离子的浓度,进而有效提高加工切缝轮廓的表面质量。
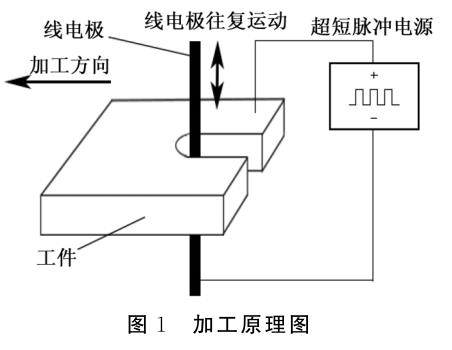
1.2试验系统
试验系统原理图如图2所示。该试验由运动系统、电解槽及线电极夹具、超短脉冲、加工观测系统、检测系统组成。运动系统采用运动控制卡控制PI高精度的三轴运动平台实现X、Y、Z方向伺服运动,可以实现0.1μm的进给分辨率和1μm的重复定位精度;X、Y轴的二维运动形成加工零件的几何形状,Z轴带动线电极进行往复运丝,加快电解产物的排出。超短脉冲的电压最大可以升高至20V,保证线电极的最大加工能力。加工观察系统主要由CCD成像,将加工区域放大,便于试验前对刀及试验过程中观察不正常现象。检测系统主要通过示波器实时检测加工过程中电流的突变,以此来判断加工过程的稳定与否。
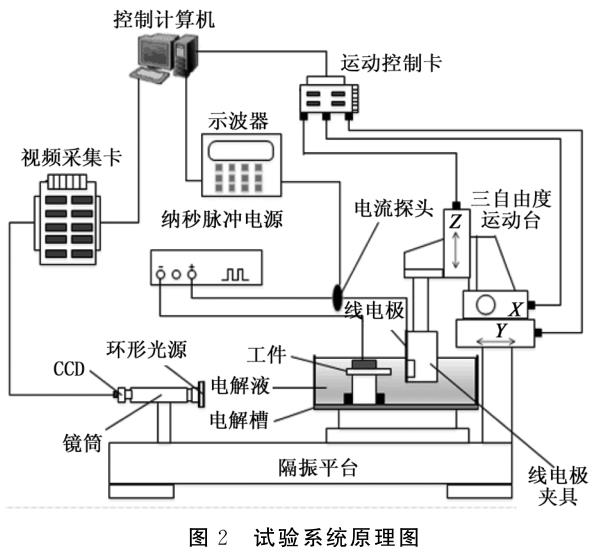
2、试验设计
本文以厚度为800μm的镍板为加工材料,以直径为10μm的钨丝作为线电极,稀盐酸作为电解液,进行微细电解线切割加工的基础试验。加工过程中,线电极进行往复运动,频率为0.3Hz,振幅为1mm。
为了研究加工电参数和电解液浓度对微细电解线切割切缝质量的影响,以加工的超短脉冲电压、脉宽、周期以及电解液浓度4个因素为研究对象,每个因素取4个水平,选用正交试验表L16(45)安排正交试验(见表1)。在每条切缝上取3个不同位置,测量3个缝宽值,取平均值L为切缝的平均缝宽,以缝宽的标准差作为评价切缝轮廓一致性的标准。分析4个因素对切缝缝宽以及切缝轮廓一致性的影响,综合考虑两者进而确定切割试验的最佳参数。
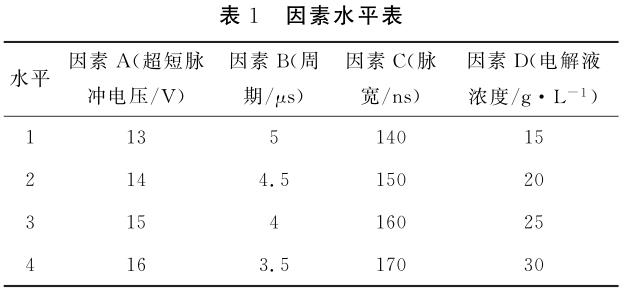
3、结果分析
3.1正交试验表切缝数据分析
正交试验表切缝数据见表2。
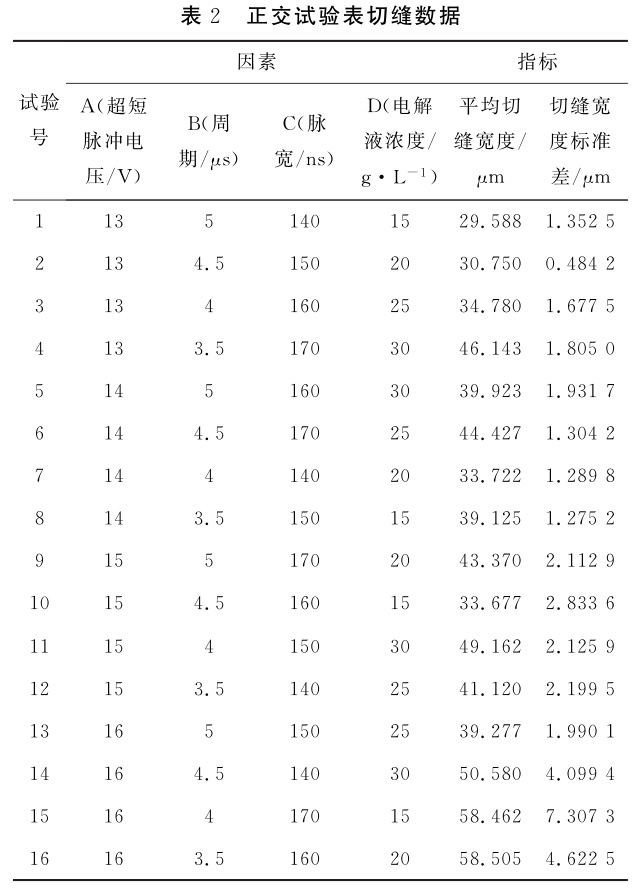
1号试验作为最小可加工参数切割宽度约为30μm,但由于此参数临近加工极限,故切缝宽度标准差不小,即切缝的轮廓均匀性没有达到非常好的效果。且由于狭缝很窄,电解产物不能及时排出,电解液难以及时更新,容易引起短路现象。
15号和16号试验的参数较大,其平均切缝宽度达到58μm左右,切缝的轮廓均匀性极差。这主要是因为加工过程中去除材料较多,相应的狭缝中产生的气泡越多,大量气泡的生成会导致线电极轻微晃动,从而加工切缝轮廓的均匀性很差。
2号试验的切缝宽度标准差仅为0.4842,远小于其他试验参数,切缝轮廓的均匀性非常好,加工过程也十分稳定。并且其切缝宽度为30.75,是除1号试验参数外最小的,非常适合作为较优加工参数进行后续加工特定的轮廓结构。
3.2正交试验的极差分析
正交试验表中,4个因素在不同因素水平条件下的平均切缝宽度以及极差大小见表3。极差的大小反应某因素的变化对平均切缝宽度的影响大小,即某因素极差越大,则该因素对平均切缝宽度影响越大,反之则越小。从表3可以看出,因素A的极差值最大为16.3840μm,其对平均切缝宽度有显著的影响,因素D对平均切缝宽度影响最小。4个因素对平均切缝宽度影响大小依次为:A(超短脉冲电压)、C(脉宽)、B(周期)、D(电解液浓度)。因此,在今后加工特定尺寸轮廓结构时,可先改变超短脉冲电压进行粗调,再改变电解液浓度进行精调,以加工出所需尺寸的轮廓。
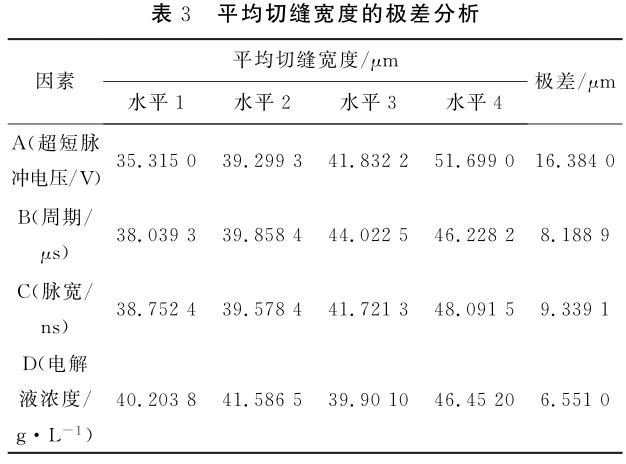
4个因素对于切缝宽度的标准差的影响大小见表4。因素A对于切缝宽度标准差的影响远大于其他3个因素。B、C、D这3个因素对于切缝宽度标准差的影响大小相似。4个因素对切缝宽度标准差影响大小依次为:A(超短脉冲电压)、C(脉宽)、D(电解液浓度)、B(周期)。
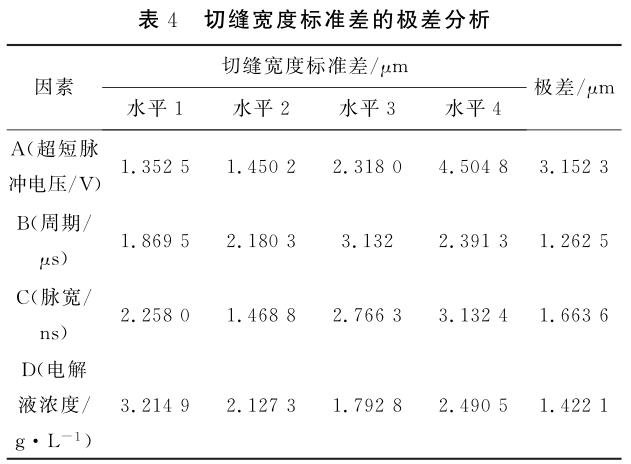
综合平均切缝宽度以及切缝宽度标准差两者的极差分析,因素A是影响2个指标的最重要因素,因素C是次要因素。而对于切缝宽度标准差,因素D相比于因素B更重要,是因为切缝轮廓的均匀性很大程度上取决于狭缝中电解液浓度的大小以及电解液的更新。
3.34个因素对于试验指标的影响趋势分析
4个因素对于平均切缝宽度以及切缝宽度标准差的影响趋势如图3和图4所示。
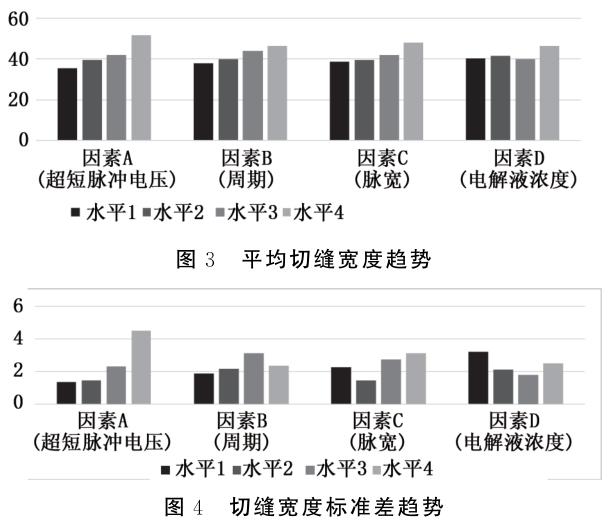
3.3.1平均切缝宽度影响趋势分析
从图3可以看出,因素A、B、C都是与平均切缝宽度正相关,随着因素D增大,平均切缝宽度先增大后减小再增大,略有颠簸,但总体呈上升趋势。随着电参数的增大,每个脉冲周期内脉冲电流对电极、溶液界面双电层充电,过电位逐渐增大,其加工能力也随之增大,自然平均切缝宽度增大。电解液主要是为电化学反应提供所需的H+离子,在电参数不变的情况下,增大电解液浓度,一定程度上也可以增大加工能力。
3.3.2切缝宽度标准差影响趋势分析
从图4可以看出,随着因素A的增大,缝宽的不均匀性也不断增大,并且相比于其他3个因素,电压对缝宽均匀性的影响作用明显更大。其主要是因为,随着加工电压的增大,双电层的电压变大,单位时间内去除材料变多,气泡变得大而多,对于钨丝线电极存在轻微的挤压变形,并且挤压变形的方向是不确定的,进而切缝轮廓崎岖不平,缝宽标准差很大。
随着因素D的增大,缝宽的不均匀性先减小后增大。电解液浓度较低时,由于切缝窄而深,仅靠线电极往复运丝难以及时更新电解液,狭缝里面电解液中H+离子被大量损耗后,加工过程变得极其不稳定,易造成短路现象,故电解液浓度较低时,缝宽的不均匀性较大。随着电解液浓度的增大,此现象得到了有效改善。同时,随着电解液浓度增大,线电极加工能力变强,单位时间产生的气泡变得大而多,故电解液浓度过大时,线电极的挤压变形现象占主导地位,影响着切缝宽度的均匀性。
随着因素B、C的增大,缝宽的标准差有增有减。其一方面是由于电参数的增大,气泡挤压线电极现象明显,另一方面气泡大而多,气泡从狭缝中上浮排出的过程又有利于狭缝中电解液的更新,故两者达到一个平衡时,切缝宽度的均匀性最好。
3.4最优参数试验分析
平均切缝宽度和缝宽标准差作为切缝试验的2个指标,前者决定切缝的宽度,后者决定切缝轮廓的均匀性和加工工件的轮廓质量,相比于前者,缝宽标准差更为重要。在切缝宽度不太大的前提下,以缝宽标准差作为主要衡量指标,根据上述结果分析选择A1B1C2D3为最佳试验参数组合。理论最佳试验参数组合下的切缝如图5所示。
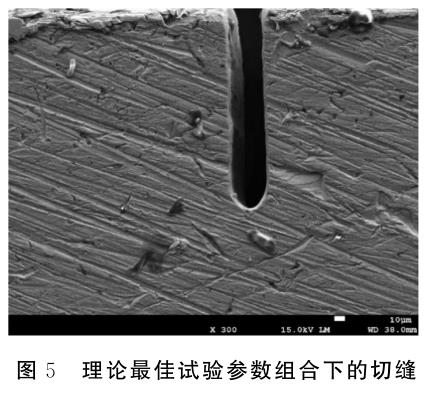
在正交试验表中16组试验参数组合下,第2组参数组合A1B2C2D2加工的切缝轮廓质量明显优于其他各组参数组合,并且切缝宽度仅为30.75μm。A1B2C2D2参数组合下加工的切缝如图6所示。与图5相比较,A1B2C2D2参数组合下的切缝轮廓更加均匀,表面质量更优。因此厚镍板微细电解线切割正交试验结果能反映各个参数对切缝质量影响的主次顺序和变化趋势,但对最优参数组合的预测存在一定的偏差。
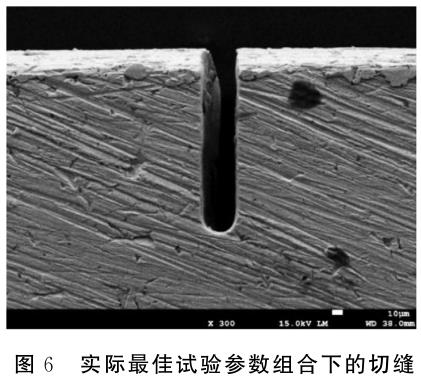
4、实际加工效果
根据上述分析,采用实际最佳试验参数组合A1B2C3D2,往复运丝幅值为1mm,运丝频率为0.3Hz,用10μm的钨丝作为线电极,在厚度为800μm的镍板上加工出悬臂梁结构(见图7)。经测量,悬臂梁长度为209.3μm,宽度为35.687μm。
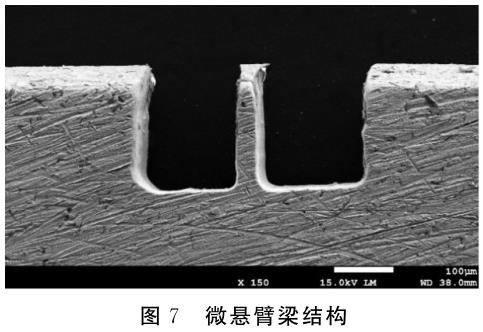
5、结语
通过上述研究可以得出如下结论。
1)超短脉冲电压相比于周期、脉宽和电解液浓度等3个因素对厚镍板切缝的平均宽度和缝宽标准差的影响更为显著。
2)切缝宽度的标准差随脉宽及电解液浓度增大,先减小后增大。为提高加工轮廓均匀性,脉宽及电解液浓度选取应适中。
3)在加工过程中,气泡的上浮过程既对线电极有挤压变形作用,又有利于电解液更新。这一过程产生的挤压变形会影响加工的稳定性,并且会增大切缝轮廓的不均匀性;但其具有促进电解液更新的作用,可以有效保证狭缝中的电解产物的排出以及电解液浓度的恒定,提高加工的稳定性以及加工轮廓的均匀性。两者存在一个最优平衡,此时切缝轮廓均匀性最好。
4)采用实际最佳试验参数组合,加工出悬臂梁结构,轮廓清晰完整。微细电解线切割技术可以加工厚零件。
参考文献
[1]RajurkarKP,LevyG,MalsheA,etal.Microandnanomachiningbyelectro-physicalandchemicalprocesses[J].AnnalsoftheCIRP,2006,55(2):643-666.
[2]SchusterR,KirchnerV,AllongueP,etal.Electro-chemicalmicromachining[J].Science,2000,289(5476):98-101.
[3]KimBH,NaCW,LeeYS,etal.Microelectrochemi-calmachiningof3Dmicrostructureusingdilutesulfuricacid[J].CIRPAnnals-ManufacturingTechnology,2005,54
(1):191-194.
[4]王少华.微细电解线切割加工技术的试验研究与应用[D].南京:南京航空航天大学,2010.
[5]MaedaR,ChikamoriK,YamamotoH.Feedrateofwireelectrochemicalmachiningusingpulsedcurrent[J].PrecisionEngineering,1984,6(4):193-199.
[6]KunioC,HideoY,RyutaroM.WireECMwithpulsedcurrent[C]//Proceedingsofthe5thInternationalConferenceonProductionEngineering.1984:407
-412.
[7]王昆,朱荻,张朝阳.微细电解线切割加工的基础研究[J].中国机械工程,2007,18(7):833-837.
[8]于洽,曾永彬,徐坤,等.阳极振动往复运丝微细电解线切割试验研究[J].中国机械工程,2014,25(3):295-299.
[9]李鹏.多线电极微细电解加工技术研究[D].南京:南京航空航天大学,2016.
[10]童品周.多层工件叠加电解线切割试验研究[D].南京:南京航空航天大学,2018.
[11]朱兵.厚不锈钢板的微细电解线切割加工技术研究[D].南京:南京航空航天大学2010.
作者简介:许银海(1998-),男,大学本科,主要从事微细电解线切割技术等方面的研究。
相关链接